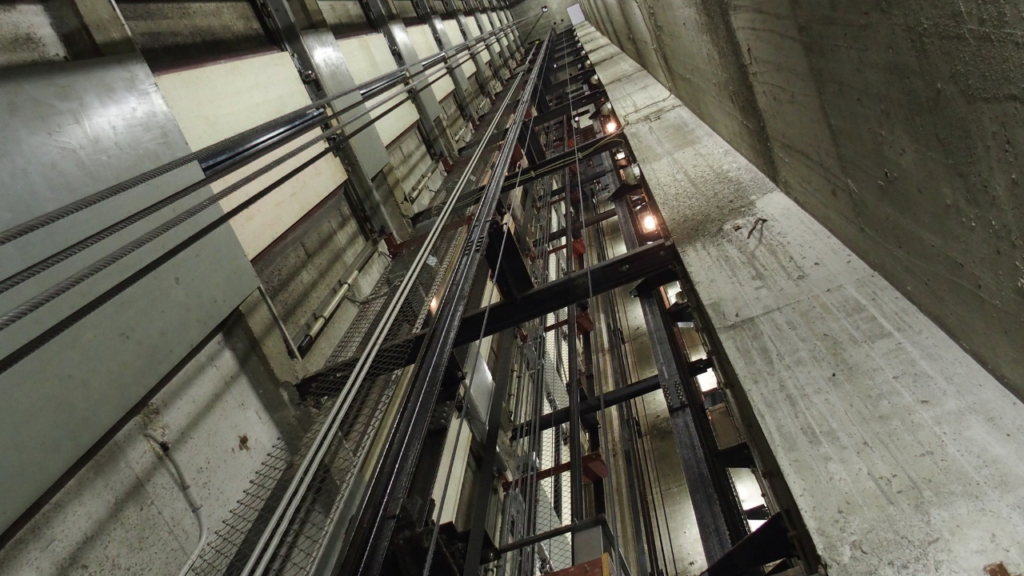
DC Motor Carbon Brushes for Elevators: Composition, Function, Solutions
The motor carbon brush has been a critical component in variable speed rotating equipment for over 100 years. The trend towards reduced maintenance has resulted in the elimination of many well established procedures related to carbon brushes. Today new technology is attempting to replace this component and permanently eliminate these maintenance costs. However, when subjected to the proper operating conditions carbon brushes do yield excellent life and perform an amazing function.