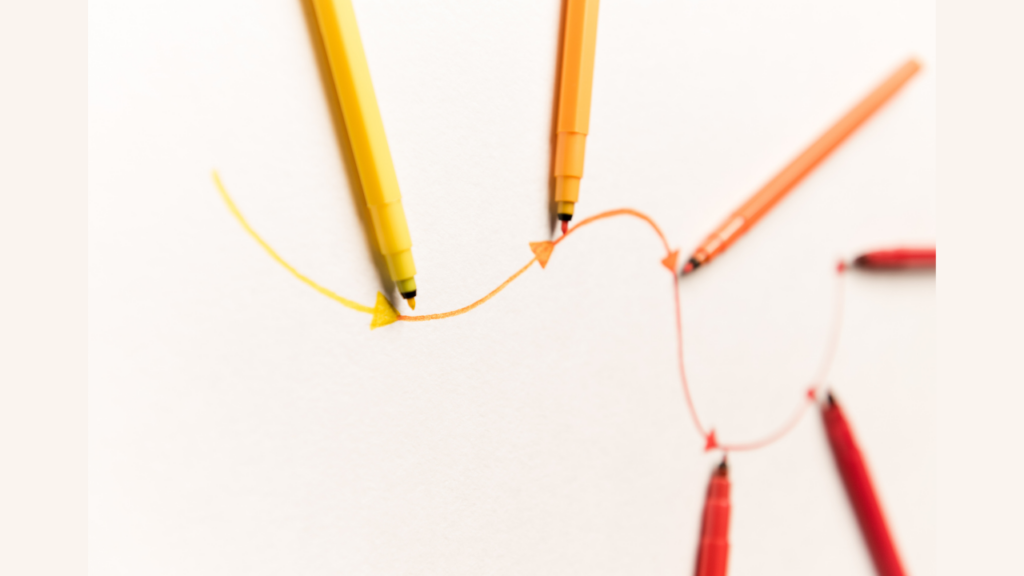
Lube Routes vs. Combo PMs: What’s Best? What are the Issues?
In an ideal world, the lube route is the perfect answer. Group activities based on commonality of frequency, task type (e.g. motor regreasing) or area of the plant and execute in one block. It’s efficient, effective and cuts down on paperwork by having just one work order for tens or even hundreds of tasks. The key here is “ideal world” – few if any of us live in this utopia, which causes some very real problems when it comes to executing what I tend to call “macro” lube routes.