Keeping Compressed Air Dry
Ted Grove, MRO-Esource
Air systems without compressed air dryers severely restrict the life expectancy of any equipment they operate. You must keep your compressed air dry.
Now that the warm weather is here, you’ve probably become complacent about your compressed air system. During the winter, water problems that plagued your compressed air system all last summer seemed to disappear. What luck, you may be thinking. You won’t have to buy that compressed air dryer. But let’s look at what actually happened to your water problem.
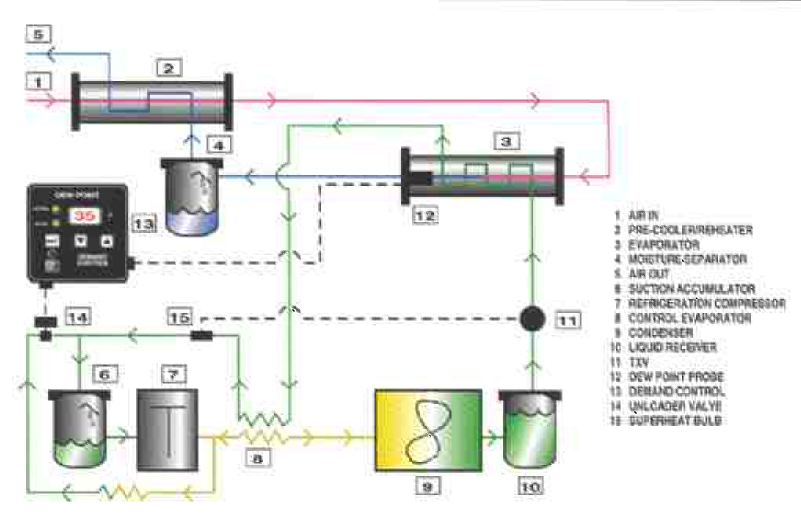
One of the most effective ways of drying compressed air is to cool it, collect the moisture that condenses, then reheat the air to the ambient temperature. That is exactly what the cool winter weather did for your compressed air system.
Remember the rules-of-thumb that were discussed in previous Ted’s Tech Talk columns. Sub-zero outside air with a humidity level of about 500% is brought inside your plant and heated, thereby reducing the relative humidity level to about 10% to 12%. When the air is compressed, the humidity level increases, but even at normal shop pressures, the dewpoint (or 100% humidity level) will seldom be reached, thus there is no apparent water problem. Rest assured, though, that this summer will bring back the water problem with a renewed vengeance.
Now is the time to consider installing a dryer, while the compressed air lines are relatively dry and any loose, flaking rust particles have been dislodged and passed downstream to be caught in the air line filters.
Three Groups of Industrial Dryers and How they Keep your Compressed Air Dry
Industrial dryers can be put into three major groups. Refrigerant and deliquescent descant dryers are used in general industrial applications, with the refrigerant units being the more effective and popular. Regenerative desiccant dryers, which used to be used only in situations requiring very low dewpoints and for instrument-quality compressed air, are fast becoming the preferred units for clean, dependable compressed air systems.
Refrigerant Dryers
Refrigerant dryers, as the name implies, cool the incoming air to a temperature or dewpoint of 1-3°C, causing a large portion of the water to condense and to be collected by a separator. The process generally uses a system of two heat exchangers to achieve this. The air-to-air heat exchanger pre-cools the incoming wet air and warms up the dry exhausting air with a very efficient and economical exchange of heat. This results in a reduced load on the air-to-freon (refrigeration) heat exchanger and also regains some of the pressure or energy lost during the cooling cycle.
It is important that the exhausting dry air be close to ambient temperature conditions to prevent water from condensing on the outside of the cool air lines and dripping on to equipment throughout the plant.
Refrigerant dryers are generally supplied with a float-type manual drain for the separator. A good installation will include a manual drain in parallel to allow frequent checks on the drainage system to make sure that it is functioning properly. Timer-operated, motorized ball valves are not affected by the gummy effluent and are thus more reliable.
Deliquescent Desiccant Dryers
Deliquescent desiccant dryers are initially cheaper to buy because they are simply large air reservoirs with a shelf installed in them to hold the desiccant bed. But because they consume the desiccant in the drying process, they are more expensive to run than other systems.
The desiccant itself is usually a salt or chloride derivative which has a stronger affinity for water than the compressed air being passed through it. The desiccant dissolves with the water and collects in the bottom of the tank so it can be drained away. It is imperative that a timed, motorized ball drain and/or manual drain be used for this system. A float-type drain will tend to clog and fail.
The dewpoints achieved with these systems are approximately 10°C below the temperature of the incoming air. Thus it is extremely advisable that these systems be used with water-cooled aftercoolers to achieve an entry temperature close to ambient levels.
Regenerative Desiccant Dryers
Regenerative. desiccant dryers use a desiccant such as silica gel to attract and absorb moisture from the air, achieving pressure dewpoints in the range of minus 40°C.
These super-dry levels allow the compressed air to be used in sub-zero conditions without ice blockages occurring outdoors. Applications include outdoor hoppers or silo gates and in automation applications in cold rooms or refrigerators This low dew-point level is also often required for sensitive instrumentation applications. More importantly, these lower dew points ensure that water never condenses in modern systems, even with the super-low temperatures achieved as the compressed air does its work.
Regenerative dryers generally consist of two identical process tanks, one which is being used while the other is being dried or regenerated. The regeneration process removes the collected water from the desiccant by lowering the pressure in the tank to atmospheric levels and drying the medium with electric heat or some of the dry air produced by the active tank.
Pre-cooling of the entry air with a water-cooled aftercooler is necessary to achieve the required operating efficiency of the dryer. Pre-filtering is mandatory to keep the desiccant contamination-free for as long as possible. The pre-filtering should include an oil removal filter to limit any chance of oil contamination of the desiccant.
Dryers are a very necessary part of an efficient compressed air system. Remember, to do work, compressed air components must consume energy, usually resulting in a pressure drop within the device. The pressure drop results in instant refrigeration of the air and the possible condensation of water within the device. The water washes away or displaces any lubrication, resulting in a severe reduction in the life expectancy of the device.
It is essential that dryers be used to ensure that the dewpoint of the compressed air is below the temperature levels reached within the working air equipment. Air systems without compressed air dryers severely restrict the life expectancy of any equipment they operate.
Read more: Drying Your Compresses Air System Will Save Real Money