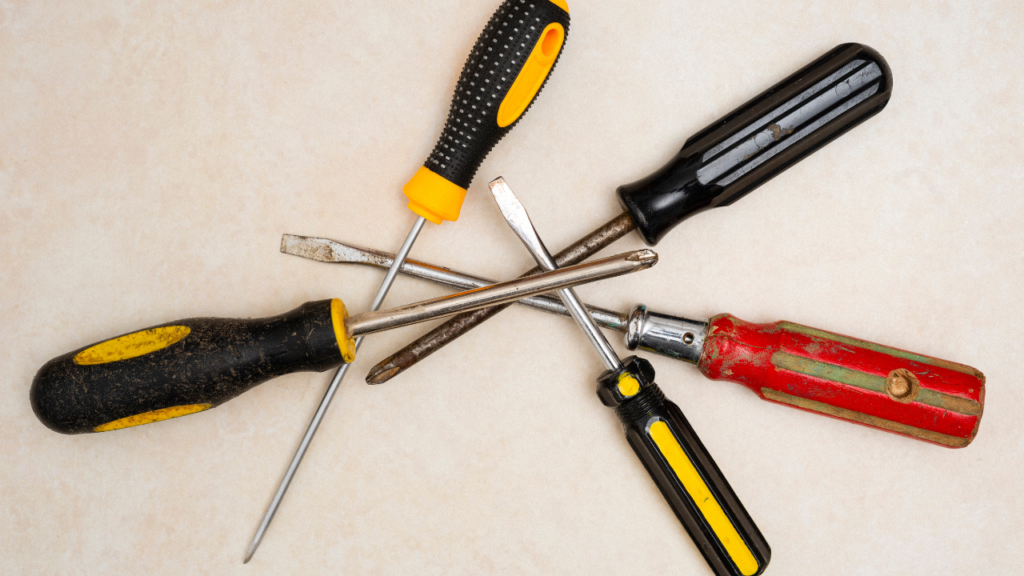
From Screwdrivers to Testers: Vibration Testing and Analysis Comes of Age
Most machines have rotating parts and those rotating parts vibrate. Measuring how and how much those parts vibrate can tell you a lot about the health of a machine. Whether it’s the rumble of worn bearings or the shaking, shimmying, or thumping of loose, misaligned, or unbalanced parts, machines have a tale to tell those who are willing and able to listen.