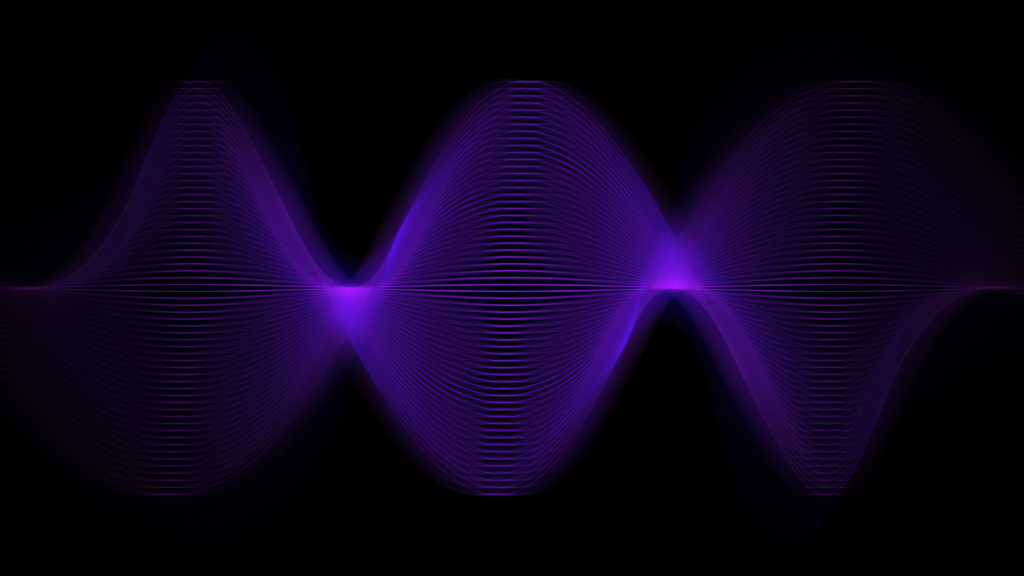
3 Ways to Improve Motor Health with Vibration Testing
It’s essential that maintenance teams focus on failure modes to match the most suitable tool to the most likely problems. Vibration analysis helps diagnose the most common faults that rotating machines are susceptible to: imbalance, looseness, misalignment, and wear. The compatible trio of owning the right tools, knowing what to test, and sustaining a functional vibration testing program can potentially reduce repair costs and limit unproductive maintenance hours.