Get Your Bearing on Brinelling
Greg Mecomber of IDCON INC, Jason Ludwig, Marlon Casey, and Dale Stallard of Regal Rexnord
Posted 03/02/2023
A conversation with Industry Leading Experts
It’s not everyday that you are lucky enough to sit and talk bearings with engineers who have a combined 85 years of experience specifically relating to the subject, but recently I was able to do just that. Let me say, they provided an informed perspective on brinelling failures, maintenance, prevention and the somewhat exaggerated “fears” that some companies use to market their products and services.
Joining me at our virtual table we have three accomplished engineers from RegalRexnord company. To my left is Jason Ludwig (Application Engineering Manager), to his left we have Marlon Casey (Engineering Manager) and last but not least to my right we have Dale Stallard (Senior Application Engineer).
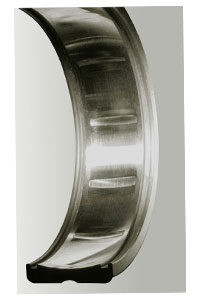
Let’s jump right into it. One of the most misunderstood types of bearing failures is Brinelling.
“Guys, tell me about brinelling. What is it and what causes it?”
Let’s distinguish a few things first, “There is true brinelling and false brinelling” Jason explains. “False brinelling is damage as a result of vibration on a bearing in a non-rotating state. True brinelling” on the other hand, “is the permanent deformation (such as dents) to the raceway. True brinelling is caused by excessive loads, excessive shock and dropping of machinery” which includes the bearing itself.
“So false brinelling is what would occur due to less than ideal storage of bearings – say lying flat on a metal shelf in a store room?”
Dale chimes in to set me straight, “Normally you have to have a significant load on the bearing for that to happen. A good example is a bearing on a piece of equipment that is sitting idle, but there is other equipment nearby that is actively creating shock waves through the concrete floor. Many don’t realize it, but you can send shock waves through a concrete floor and it causes a very small amount of vibration in the idle equipment that is then transferred to the bearing.” As Dale is saying this, I’m reminded of drowsy nights sitting in the breakroom of a metal stamping plant captivated by the ripples in my cup of coffee as it sits on the table. “Transporting cars by rail is another example” he continues, “Years ago automobiles were commonly transported by rail, and they weren’t tying them down well. The cars would bounce around and the wheel bearings would get damaged. A bearing sitting unmounted in a box on a shelf generally isn’t’ going to cause a problem.”
“Those are good examples of what brinelling is, but what effect does it have on my equipment and how does it manifest itself”, I wonder.
“Speaking specifically about bearings” Dale points out, “you’re creating defects on the raceways – the contact surfaces of the bearing. Let’s say you have some true brinelling where you have an indentation on the roller; every time there is rotation and the roller makes contact with the inner and outer race it will cause a vibration and vibration manifests itself into noise – so, you’ll hear this thing. If it’s bad enough, it will sound like a freight train running down the tracks.” (I’m Imagining the familiar clack clack… clack clack… clack clack I’d inevitably hear when I’m already late for work.) “I mean… they can REALLY rumble” he says. “The other thing is that these damaged areas will disrupt the lubrication film in the bearing and that leads to extremely high stresses in the material which will result in a premature bearing failure.”
“It could create heat too” Jason points out.
“So, not something you would have to have ultrasound equipment to detect” I noted.
“If it’s significant enough, that is correct; there will be signs and symptoms.” Jason pauses. “Taking vibration readings is another way of diagnosing a problem. It will show up on a vibration analysis spectrum as excessive vibration coming from the bearing which would indicate that there was something wrong, but they likely wouldn’t be able to diagnose it as false or true brinelling.
I suggest “At which point it would be wise to replace the bearing and use the damaged bearing to perform an RCA or RCPE to address and eliminate the cause of the damage and prevent it from reoccurring in the new bearing.”
“And that kind of condition monitoring” Dale claims, “will detect a failure much much sooner than when you are able to hear an audible noise. Because the vibration signature is much more … sensitive to picking up damage in the bearing. Which is why more and more people are using it in industry today.”
“For the earliest detection, would you be able to use something like a vibration pen or would something more sophisticated need to be used” I inquired of Dale.
“It’s kinda hard to say. When you’re taking a vibration reading it doesn’t matter where you take it. You can take it on the bearing or on the piece of equipment. It doesn’t care where the vibration is coming from – if there is vibration in the system it picks it up. The thing that you have to be able to do is differentiate the frequencies of that vibration. For instance, a bearing has four natural frequencies to it; if there is a defect on a roller, that will show up as a certain frequency. If your vibration device isn’t capable of mapping out those different vibration frequencies, then all your device is doing is telling you the level of vibration without any indication of the origin or cause. A skilled technician and a sophisticated analysis device” Dale explains, “can pin point where the vibration is coming from and pin point it to a bad raceway.”
“What are some of the worst issues you guys have seen result from severe brinelling?”
Dale prefaces his response, “Like we mentioned, it disrupts the oil film.” This kind of damage is exponential and can occur rapidly. “It can get to the point where the bearing develops so much heat that it locks itself up and – something has to give. I’ve seen shafts that were twisted like a pretzel because a bearing locked up. You can have anything from just a noisy bearing to a complete destruction of a piece of equipment!”
“Just depends on how long you let it go” Jason says coolly.
“Yeah!” Dale agrees. “If it’s on an application that has nobody around it – nobody can hear it, nobody can smell it and it will just continue until it can’t any longer.”
Marlon states matter of factly, “brinelling could potentially reduce the remaining life of the bearing by up to 50%.”
“Can this happen to all bearings” I ask Marlon. “Are some materials worse than others?”
“The amount of brinelling will be the same, but the effect it has on fatigue strength can be different depending on the type of material from which the bearing is made.”
“Well, is there anything we can do to fix or prevent it?”
An excited Dale responds, “You can’t fix a brinelled bearing. To prevent it, basically remove everything that we’ve said that causes it. Don’t drop bearings, don’t drop equipment, don’t subject equipment to vibration while it is sitting idle. If a piece of equipment HAS to sit idle, you do things to isolate it; you put it on rubber mounts…”
“Isolated concrete pads!” Jason exclaims.
“Yeah!” Dale agrees. “Obviously vibration isn’t anything new, people have had to deal with it in applications for years. I think people are getting better at finding ways to deal with it. Anything to isolate that piece of equipment from outside sources of vibration. The true brinelling mark comes from impact loading.”
The energy level continues to rise as Jason picks up the conversation. “Always applying force to the part that is being press fit onto the shaft. So, if you have to force a bearing’s inner ring onto a shaft – force the inner ring on, don’t hit on the outer ring as that could put indentations onto the raceways. We also talked about the transportation of equipment; one way to prevent brinelling while transporting is to properly block the shafts during shipment, so that the bearing and rolling elements don’t sit there and vibrate and cause that false brinelling damage.”
“An interesting thing” Dale muses “that seems to go against that thinking is, we provide bearings to a lot of fan and blower manufacturers and, if you can do it safely, they will actually let the fan wheel free so that when it’s being transported down the highway … you’ll see the fan turning just from the air as it is going down the highway. And THAT’s actually a good thing because it keeps the bearing moving … it helps prevent that brinelling. But, that is kind of an unusual case because most applications can’t turn while it’s being transported.”
“In that respect,” I comment “one of the things you’re supposed to do is rotate a motor shaft every few months. I’ve always been told this is to prevent this type of damage as well.”
“It can be. That would be more to prevent false brinelling” Dale specifies. “Because what happens is you have a separating oil film between the rollers and the raceways and if that over time is deteriorated, you start to have direct metal to metal contact and that’s when the false brinelling takes place. By rotating a shaft, you redistribute the lubricant in the bearing and you restore that lubrication film between the surfaces. That’s definitely one way to prevent it. Normally … when people are rotating shafts [it] is on a piece of stationary equipment to prevent condensation forming in the voids due to temperature changes and which will attack the raceways. Because gravity causes the lubrication to run to one point you can get condensation to form inside a bearing. You could rotate a bearing for multiple reasons – and to try to eliminate or reduce the effects of brinelling would be one of those.”
“Do you guys have any recommendations on how to improve bearing performance in general?”
The crowd erupts, “Mount it right and lubricate it!”
Everyone spouting their personal suggestions, Jason’s voice rose above the others. “Getting it mounted correctly and keep it lubricated properly! Those are the two main causes of bearing failure. More specifically, proper lubrication intervals and the amounts are important, using the right grease – there is no one perfect grease – using the right seals for the environment the bearing operates in to keep contaminants out of it. Following the proper installation steps, having the right shaft tolerance, making sure the bearings are properly aligned…”
“Alright… alright… everybody settle down” I joke. “Last question. Are some environments worse for brinelling than others?”
Ever mellow, Marlon stylishly lowers his cup of coffee and picks up the conversation from the others. “Humid and corrosive environments for false brinelling. For true brinelling, applications with a lot of shock loading, such as conveying heavy materials, having materials dumped onto a conveyor system such as tree logs or boulders.”
As my time with them came to an end, we all went our separate ways and I was keen to ponder some of the key points from our conversation.
- There are two types of brinelling: True and False. True brinelling generally comes from impacts and shock loads while False brinelling comes from vibrations on a stationary bearings with a significant load.
- Mount it right and lubricate properly!
- Vibration during bearing storage is less of a contributing factor to bearing degradation than temperature, humidity and cleanliness.
- Rotating motor shafts is more for redistributing lubricant film within the bearing than for directly preventing brinelling of either kind.
- If you have severe brinelling, you will know it due to the sound of a train going down the tracks.
- Sophisticated vibration analysis systems can detect and diagnose specific failures and which parts of the bearing has failed long before the bearing has a chance to damage other equipment or shut down operations.
- Avoid introducing shock loads or dropping machinery. In the words of Val Rosing, “Try a little tenderness.”
- When in the design and planning phase, especially in facilities with a great deal of shock waves, consider ways to isolate equipment to prevent damage and extend the life of your bearings.
Jason Ludwig
Jason Ludwig is the Application Engineering Manager for Rexnord’s Bearing Division. He has been with Rexnord since 2005 in roles of increasing responsibility. Jason works closely with Rexnord’s customers helping to troubleshoot issues, provide onsite support, train personnel, and select bearings that fit the customer’s needs. As the Application Engineering Manager for Rexnord Bearings, he is an expert on all bearing products that Rexnord provides.
Marlon Casey
Marlon Casey is an Engineering Manager with the Rexnord Bearing Group. He has spent 11 years with Link-Belt and over 31 years with Rexnord managing the Research and Development Testing, Engineering Analysis, Product Design and Development and Product Engineering activities. Marlon’s responsibilities include conceptualizing, developing, maintaining, and improving bearing products required to support MB, Link-Belt, REX and Filament Industrial Bearing products. His skillsets and vast experience are regularly utilized by the manufacturing commercial, and applications’ departments to provide an expert level of product knowledge to support customer needs.
Dale Stallard
Dale Stallard started with Rexnord in 1988 and has held different positions in Quality Control and Product Design and Development at multiple facilities. Dale is a Senior Application Engineer supporting Rexnord’s bearing business. In his current role, he provides customers with support such as helping them select the proper bearing, onsite assistance, maintenance and installation training, and troubleshooting with any issues.
Greg Mecomber
Greg Mecomber is a reliability and maintenance consultant. He has years of maintenance and reliability experience with both “turn-around” and start-up companies as well as experience in varied industries such as brewing, medical devices, glass fabrication, airfield maintenance and food & beverage.