Talent Shortage Among Maintenance Professionals and How a CMMS Can Help
Reena Sommer, Ph.D. for Click Maint CMMS
Posted 2/18/2025
Introduction
The maintenance sector is currently facing a severe talent shortage. As a result, various industries that rely on skilled maintenance professionals are being impacted. This maintenance talent shortage is traced to several factors, including an aging workforce, a lack of incoming skilled workers, and evolving technological demands.
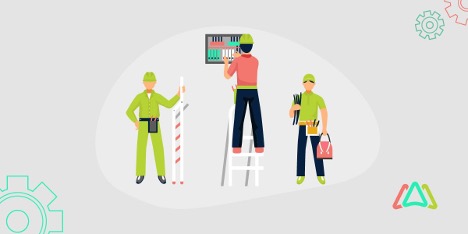
Key Statistics Illustrating the Maintenance Talent Shortage:
- General Maintenance and Repair Workers: The U.S. Bureau of Labor Statistics projects about 157,200 job openings annually for general maintenance and repair workers from 2023 to 2033. These openings are primarily the result of workforce exits and transfers.
- Industrial Machinery Mechanics and Maintenance Workers: Employment in this sector is expected to grow by 15% from 2023 to 2033, significantly outpacing the average for all occupations. The projected growth equates to approximately 53,000 job openings each year and is driven by the need to replace retiring workers and those transitioning to other roles.
- Automotive Technicians: The Bureau of Labor Statistics anticipates over 67,000 annual job openings for automotive technicians between 2022 and 2032, underscoring the high demand in the automotive maintenance sector.Â
Aviation Maintenance Technicians: In 2021, the median salary for aviation maintenance technicians in the U.S. was over $65,000, with some states reporting even higher averages. Despite competitive wages, the industry faces challenges in attracting sufficient qualified personnel.
These industry statistics highlight the increasing need for effective strategies to address the maintenance talent shortage. Implementing solutions such as investing in training programs, enhancing recruitment efforts, and leveraging technology like Computerized Maintenance Management Systems (CMMS) can play a pivotal role in mitigating this challenge. Here, we’ll focus on CMMSs as a vehicle for filling the gap in maintenance talent shortages.
Understanding the Causes of the Maintenance Talent Shortage
Before exploring how CMMSs can mitigate the shortage of maintenance talent, let’s examine the reasons for it a bit more deeply.
Aging Workforce and Lack of Younger Skilled Workers
Many experienced maintenance professionals have spent years working in their roles and are nearing retirement, creating a significant void in the workforce. The U.S. Bureau of Labor Statistics notes that the average age of maintenance workers is increasing, and replacements are not entering the field at the same rate, creating a gap. Younger generations are often drawn to other careers, such as technology, healthcare, or finance, instead of skilled trades.
Skills Gap Due to Evolving Technology
Advancements in technology, such as automation, Internet of Things (IoT), and predictive maintenance, have transformed the maintenance industry. While these innovations improve efficiency, they also require a workforce with specialized technical skills. Many current workers lack training in these new technologies and may be reluctant to acquire them. The same is true for the bank of potential who lack sufficient hands-on experience, exacerbating the skills gap.
Competitive Job Market and Employee Turnover
As a result, highly skilled maintenance professionals are in demand across the manufacturing, healthcare, transportation, and energy industries. This demand results in high turnover rates, as skilled workers often leave for better-paying positions or companies offering more attractive benefits. Additionally, physically demanding work conditions and irregular hours frequently contribute to burnout, making it more challenging to retain skilled maintenance professionals.
Lack of Formal Training Programs
Further to the point of acquiring skilled maintenance professionals, many companies struggle to find qualified candidates due to declining vocational training programs and apprenticeships. Over the years, there has been a societal shift away from skilled trades education in favor of four-year college degrees. Without sufficient investment in technical education and on-the-job training, fewer workers are entering the maintenance field with the necessary expertise.
Practical Steps to Address the Maintenance Talent Shortage – How a CMMS Can Help
A CMMS software can be crucial in overcoming the challenges that accompany talent shortages by automating tasks, improving training, optimizing workforce utilization, and reducing operational inefficiencies. Here are a few practical steps organizations can take with the assistance of a CMMS.
Improve Workforce Recruitment and Retention
The key to retaining or attracting maintenance talent is for companies to offer attractive work environments, competitive salaries, and career development opportunities to keep employees engaged and motivated. A CMMS can help with:
- Optimized Workload Distribution:Â CMMS aids with talent retention by allowing maintenance managers to assign tasks more efficiently, prevent worker overload, and reduce burnout.
- Performance Tracking and Career Growth: CMMS systems’ ability to track technician performance and work history provides data that identifies top performers who deserve promotions or additional training.
- Incentivizing High Performance:Â CMMS reports can help organizations create performance-based employee incentives, such as bonuses for completing preventive maintenance on time.
Invest in Training and Upskilling
Many organizations have a difficult time finding candidates with the necessary technical skills. As an alternative to waiting for skilled workers to enter the job market, companies can invest in training and upskilling their current workforce to bridge the skills gap. A CMMS can help with:
- Centralized Training Documentation:Â A CMMS can store instructional materials, manuals, and SOPs (Standard Operating Procedures), making it easy for new hires to access training resources.
- Tracking Employee Certifications:Â A CMMS can help track employee certifications and training progress. This capability ensures that all technicians are appropriately qualified and compliant with industry regulations.
- Guided Workflows for On-the-Job Training:Â A CMMS can provide step-by-step digital checklists and work order instructions. This aid helps newer technicians follow structured maintenance procedures under supervision.
Optimize Workforce Efficiency with CMMS
Maximizing the efficiency of a company’s existing team is critical, given the smaller pool of available workers. A CMMS helps streamline operations by automating scheduling, prioritizing urgent tasks, and minimizing downtime. A CMMS can help with:
- Automating Preventive Maintenance (PM): CMMS can schedule PM tasks to reduce unexpected breakdowns rather than relying on reactive maintenance. This allows technicians to focus on planned work rather than emergency repairs, bolstering preventive maintenance.
- Work Order Prioritization:Â A CMMS categorizes and prioritizes maintenance tasks based on urgency, ensuring that critical work is handled first without overwhelming the workforce.
- Mobile CMMS Access:Â With mobile CMMS functions, technicians can receive and close out work orders from anywhere using their mobile devices. This feature reduces time wasted on unnecessary trips back to the office to update the system.
Leverage Data for Better Decision-Making
Data-driven decision-making helps maintenance teams utilize resources efficiently by identifying areas where workforce gaps can be minimized. A CMMS can help with:
- Predictive Maintenance with Data Analytics:Â A CMMS collects equipment performance data to predict failures. This feature makes proactive maintenance planning possible, and in doing so, it reduces unexpected workload spikes.
- Resource Allocation Optimization:Â CMMS insights help identify overworked teams and areas requiring additional staff or training.
- Cost and Labor Tracking:Â With a CMMS, companies can determine whether outsourcing tasks or hiring additional staff is needed by analyzing maintenance costs and labor efficiency.
Reduce Knowledge Loss with Digital Documentation
As experienced workers retire, organizations run the risk of losing valuable knowledge that is not documented correctly. A CMMS acts as a knowledge repository by preserving critical maintenance expertise. A CMMS can help with:
- Storing Maintenance Best Practices:Â Organizations can document troubleshooting guides, repair instructions, and lessons learned within the CMMS. Making this information accessible to new hires helps ensure they have the most valuable resources at their fingertips.
- Digitized Work History:Â CMMS keeps detailed records of past maintenance work, allowing technicians to review previous issues and solutions without relying on verbal knowledge transfer. Utilizing this feature helps keep technicians informed and prevents the stress and frustration that contribute to burnout.
- Interactive Learning Tools:Â Some advanced CMMS platforms integrate with augmented reality (AR) or instructional videos. These features provide technicians with real-time guidance for complex repairs.
Conclusion – Maintenance Talent Shortage
The maintenance talent shortage is an ongoing challenge for many company stakeholders and maintenance managers. The gap in available talent impacts equipment uptime, operational costs, and safety compliance. However, when organizations embrace technology-driven solutions like CMMS, these changes can be mitigated by automating workflows, optimizing technician productivity, and preserving institutional knowledge.
To stay ahead, maintenance managers must assess their current processes and identify areas for automation. Company stakeholders should view CMMS adoption as a long-term investment in operational stability. Now is the time to modernize and explore CMMS solutions and future-proof maintenance operations.
Reena Sommer
Reena Sommer has written extensively about CMMS and maintenance management best practices since 2018. Reena has been a contributor for Hippo CMMS, Click Maint among others. She has her Ph.D. in Psychology from the University of Manitoba. Reena hails from Winnipeg, Canada and currently resides in Chicago, Illinois, USA.