Streamlining Work Order Management for Improved Facility Operations
Jeff Roscher, CEO, eWorkOrders
Posted 1/16/2025
Maintaining seamless operations at facilities, improving maintenance procedures, and reducing downtime all depend on efficient work order management. Organizations can greatly enhance their ability to prioritize activities, expedite work completion, and optimize overall workflows by putting strategic methods into practice and leveraging contemporary solutions, such as Computerized Maintenance Management System (CMMS) software. This thorough article provides facility managers with the necessary tools to become proficient in work order administration and maximize maintenance operations.
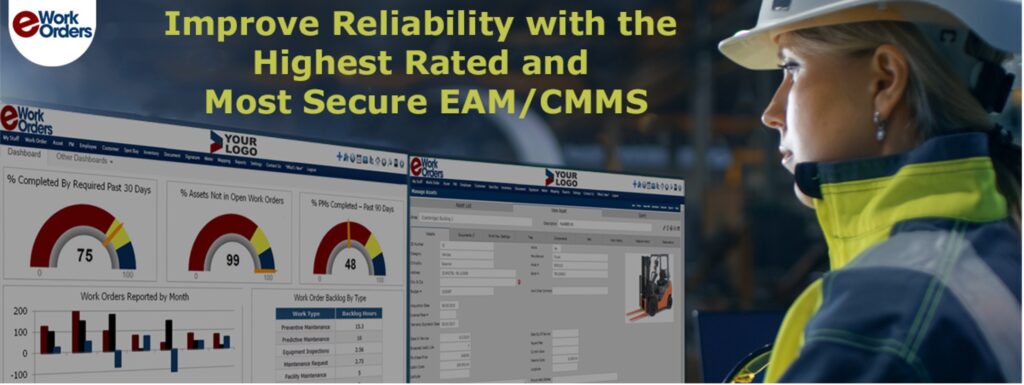
The Value of Effective Work Order Administration
The foundation of maintenance operations is work order management. It includes planning, allocating, monitoring, and finishing maintenance work. In addition to guaranteeing that activities are finished on schedule, an effective work order management system improves resource utilization, lowers operational downtime, and preserves overall facility performance.Â
Key Benefits of Effective Work Order Management
- Increased Productivity: Maintenance crews may concentrate on important work without needless delays thanks to streamlined procedures.
- Resource Optimization: Effective management results in more efficient use of resources, guaranteeing that the appropriate staff and equipment are available when needed.
- Less Downtime: Equipment failures and service interruptions are reduced when work orders are completed on time.
- Better Communication: Team members and stakeholders communicate more effectively when using a structured task order system.
Key Components of the Work Order Management Process
To create an effective work order management system, it is crucial to understand its key components:
Request Process
The process begins with a standardized system for submitting maintenance requests. This system should capture essential information such as:
- Requester contact information
- Asset identification
- Location
- Description of the issue
- Urgency level
Requests should be triaged to assess urgency and resource requirements. Integrating this process with a Computerized Maintenance Management System (CMMS) facilitates automated tracking and enhances oversight.
Work Order Generation and Detailing
Once a request is received, a comprehensive work order is generated. This work order should include:
- Task description
- Scope of work
- Asset details
- Priority level
- Required skills and competencies
- Necessary tools
- Estimated completion time
Providing detailed information ensures clarity and efficiency in task execution.
Planning and Scheduling Optimization
Effective planning and scheduling are vital for maximizing operational efficiency. Work orders should be prioritized based on:
- Human safety
- Asset criticality
- Operational impact
- Resource availability
Utilizing advanced scheduling tools helps ensure optimal resource utilization while integrating preventive maintenance tasks into the workflow.
Work Execution and Monitoring
Skilled technicians execute maintenance tasks using the necessary resources. Real-time progress tracking allows for monitoring task completion against established timelines. Any deviations or additional requirements should be documented for accurate reporting.
Completion Verification and Documentation
Upon task completion, a thorough review ensures that quality standards are met. Documentation should include:
- Detailed reports
- Photographic evidence (if applicable)
A formal sign-off process involving all stakeholders is essential before closing the work order in the CMMS for future reference.
Performance Analysis and Continuous Improvement
The final step involves analyzing completed work orders to identify trends and review key performance indicators (KPIs). This analysis informs refinements in maintenance strategies based on historical data, leading to continuous improvement initiatives that enhance overall effectiveness.
Optimizing Work Order Workflows
To improve work order management further, consider implementing the following strategies:
Standardize Work Order Formats
Using standardized templates ensures consistency across tasks, helping maintenance teams execute work more efficiently. A uniform format allows for easier tracking and reporting.
Implement a Prioritization System
Establishing a clear prioritization system ensures that critical tasks are addressed promptly. Categories might include:
- Low Priority: Non-urgent tasks that do not impact operations.
- Medium Priority: Tasks necessary for smooth operations but not critical.
- High Priority: Critical tasks essential for facility operations.
Leverage CMMS Tools for Task Assignment
Technicians can be assigned tasks according to their location, availability, and skill set thanks to CMMS technologies. This improves efficiency by lowering misallocation-related mistakes.
Automate Work Order Generation
Automating routine work order creation within the CMMS ensures consistent scheduling and execution of preventive maintenance tasks while reducing manual effort.
Enhance Mobile Accessibility
Mobile CMMS solutions allow technicians to access work orders, update statuses, and log completions in real-time. This capability improves productivity by enabling quick responses to emerging issues.
Implement a Multi-Factor Prioritization Approach
Use a multifaceted strategy to prioritize work orders by considering factors such as:
- Equipment criticality
- Safety implications
- Regulatory requirements
- Production impact
- Resource availability
This thorough method guarantees that when setting priorities for jobs, all pertinent aspects are taken into account.
Utilize CMMS Analytics for Data-Driven Decisions
CMMS analytics can identify trends, highlight recurring issues, and provide insights into resource allocation. By leveraging data-driven insights, organizations can make informed decisions about task prioritization and resource management.
Balance Preventive and Reactive Maintenance
Maintaining a balance between preventive and reactive maintenance is crucial for addressing both urgent repairs and ongoing equipment upkeep. A proactive approach minimizes unexpected failures while ensuring that regular maintenance is performed on schedule.
Implement Skills-Based Assignment
Match work orders with technicians based on their skills and certifications to ensure efficient, high-quality task execution. This strategy not only improves task completion rates but also enhances technician satisfaction by aligning their expertise with job responsibilities.
Reducing Response Times and Minimizing Facility Downtime
Minimizing response times is essential for reducing downtime in facility operations. Consider implementing the following strategies:
Automated Notification Systems
CMMS can automatically notify relevant personnel of high-priority work orders, ensuring rapid responses to critical issues. Timely notifications help prevent minor problems from escalating into major failures.
Establish Clear Escalation Procedures
Develop clear escalation procedures to quickly address complex or time-sensitive maintenance issues. A well-defined escalation protocol ensures that urgent matters receive immediate attention from appropriate personnel.
Optimize Inventory Management
Tracking inventory levels within your CMMS allows for automated reordering of commonly used parts. Ensuring that essential components are always available reduces delays caused by material shortages during maintenance activities.
Regular Training and Skill Development
Ongoing training programs enhance technicians’ expertise and familiarity with equipment, improving response times and overall efficiency. Investing in skill development fosters a culture of continuous improvement within the maintenance team.
Implement Predictive Maintenance Strategies
Utilize sensors and analytics to predict potential failures before they occur. Predictive maintenance allows organizations to perform proactive interventions based on data insights rather than reactive responses to equipment breakdowns.
Streamline Communication Channels
Centralized communication platforms within the CMMS improve real-time collaboration among team members. Effective communication reduces delays caused by misunderstandings or lack of information during maintenance activities.
Leveraging CMMS for Continuous Improvement
A well-integrated CMMS system drives continuous improvement in facility operations through several key strategies:
Monitor Key Performance Indicators (KPIs)
Effective performance evaluation is made possible for businesses by monitoring important indicators including work order completion rates, Mean Time to Repair (MTTR), and average response times. KPIs can be reviewed frequently to help pinpoint areas that need improvement.
Implement a Feedback Loop
Encouraging technician feedback on work orders allows organizations to identify challenges faced in the field. Gathering insights from frontline workers helps refine processes and update maintenance procedures accordingly.
Conduct Regular Process Reviews
Regular evaluations with key stakeholders help uncover bottlenecks in workflows or areas where improvements can be made. Engaging various team members ensures diverse perspectives are considered during process reviews.
Leverage Historical Data for Planning
Using historical data captured by the CMMS enables organizations to optimize future maintenance strategies based on past performance trends. Analyzing historical data informs better resource allocation decisions moving forward.
Integrating Work Order Management with Other Business Processes
Work order management does not exist in isolation; it intersects with other critical business functions that enhance overall operational effectiveness:
Inventory Management Integration
Making sure that the parts you need are accessible when you need them depends on efficient inventory management. Real-time stock level tracking and automated restocking procedures based on impending work orders are made possible by integrating inventory management with work order systems.
Asset Management
Work order management and asset management system integration offer insight into asset lifecycles. By combining information from both systems, predictive maintenance plans may be improved and asset usage can be maximized over time.
Customer Service
By reducing service interruptions brought on by equipment failures or maintenance delays, effective work order management improves customer service. Positive word-of-mouth recommendations and greater loyalty are the results of happy customers.
Conclusion
Optimizing work order management requires strategic planning, effective use of technology, and continuous refinement of processes. By standardizing workflows, leveraging CMMS tools for task prioritization, minimizing response times, and integrating various business functions, organizations can significantly enhance their facility operations.
Success stems from viewing work order management as a dynamic process that adapts to evolving needs within an organization’s operational landscape. Ongoing assessments driven by data insights ensure long-term operational success while fostering a culture focused on continuous improvement.
Jeff Roscher
Jeff Roscher is the Co-Founder and President of eWorkOrders, a leading provider of Computerized Maintenance Management System (CMMS) and Enterprise Asset Management (EAM) software. With his extensive technological expertise and sharp insights, Jeff has established himself as an innovator in the field, creating customized and cost-effective solutions for companies of all sizes. Under his leadership, eWorkOrders has become an industry leader in CMMS and EAM software.
To learn more about eWorkOrders and their software solutions, visit their website at https://www.eWorkOrders.com Â