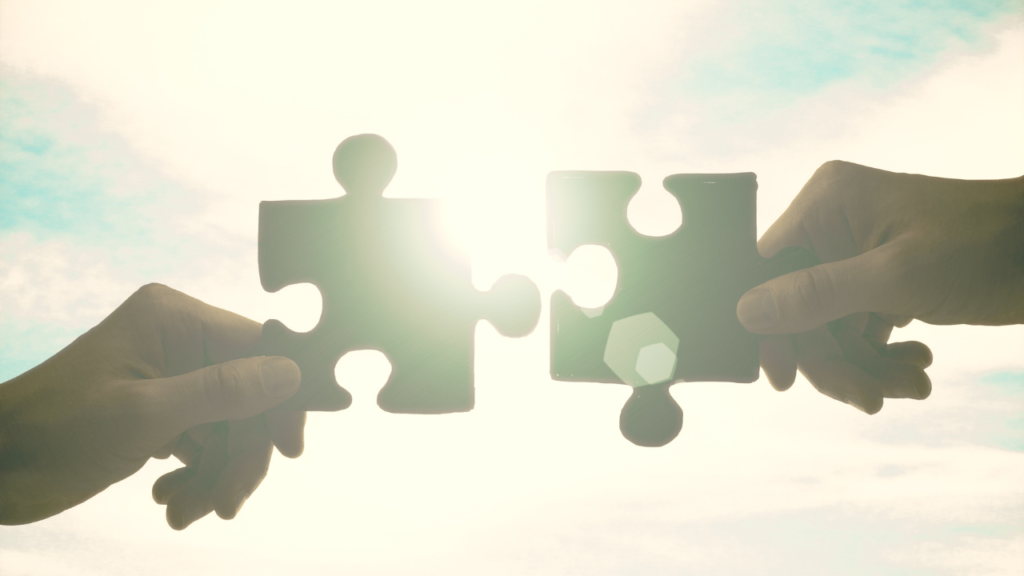
Beginning a Maintenance and Operations Partnership
Plant pros often talk about the importance of a maintenance, operations and engineering partnership. In my experience, the discussions commonly center on very general terms such as better communication and understanding. Those issues are important, but we need precise rules and actions to drive that partnership long term.